Written by Lewis Wing
Introduction
With an increasing customer expectation to receive items in extremely short timeframes, warehouse design and logistics optimisation has never been more important. Companies like Amazon have set a new standard with Amazon prime and demonstrated the possibilities of same day or even same hour delivery.
Given such a wide range of solutions and a huge amount of potential to optimize warehouse performance, why aren’t more companies doing more to optimise their warehouse performance? The simple solution is capability and know-how. Many of the technological based solutions are not understood well enough or simply not known by warehouse managers. Additionally, upon the adoption of warehouse optimization, companies often are unaware of performance measures and how the details of their warehouse operations translate into cost and service performance.
This article provides a scatter of ‘things to consider’ when optimising a warehouse. This article is not a complete guide but more food for thought, to help question the current way of working and understand what good looks like.
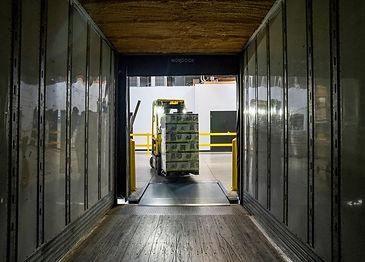
What is Warehouse Design?
•Design of layouts and operation standards in order to minimise waste;
•Optimisation of the inbound and outbound flows in the warehouse.
•Minimisation of handling & movements
•Utilising space (volume) efficiently
​
The underlying principle of warehouse design should be to minimise handling & movement
​

Benchmarking
Understanding the significant cost reduction potential is a common theme when speaking with warehouse managers or business owners. There is a large gap in knowledge and awareness of what good looks like in warehousing. First and foremost, many companies don’t look at their data to give them insights relating to how much the average item costs to store, pick and deliver. Benchmarking by comparing warehouses is often inaccurate due to the differing services, # SKUs, order patterns, supply chain requirements etc. As with many lean transformations, when assessing the potential improvements, a cleansheet approach is required. What this means is that a current breakdown of all the current individual costs will be made into something called a value tree. This value tree will then be compared with a LPC (lowest possible cost) value tree, identifying the lowest cost of each component based on each companies needs and specifics.
This comparison between ‘current state’ and ‘future state’ will provide a guide for where the largest improvements can be made as well as a target to aim for. The key to understanding the potential savings is to ensure a full picture of the operations is understood, with a through set of data collected and a scenario-based analysis conducted that avoids oversimplification by using averages. The common mistake of using averages or not truly understanding all the relevant metrics can have a detrimental effect to performance.
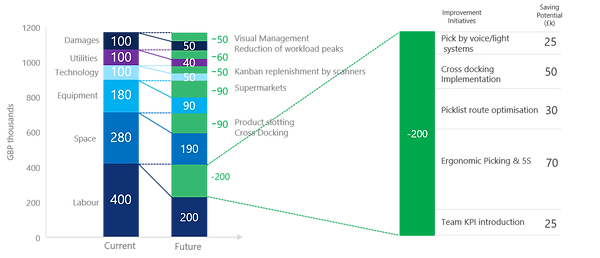
The example case above shows the current state of a warehouse costing £1.1m, broken down into 6 main categories; Labour, Space, Equipment, technology, Utilities & Damages.
The analysis shows that roughly 50% of the current cost could be saved, with the main contributor being labour savings. A further breakdown of labour savings shows how Ergonomic picking & 5S implementation could save £70k and cross docking implementation could save £50k. This preliminary benchmarking analysis provides the basis for an improvement roadmap as well as KPIs to be generated. A key thing to note; the precision of the numbers at this stage is not vitally important, it acts as an insight as to where the biggest improvement areas are and rough estimates to their magnitude, more accurate estimates will be calculated during the roadmap and strategy stage, the benchmarking provides direction as to where to focus.
Guiding Principles - Top 11 Warehousing Principles
The following list of principles help act as reminders and ‘back to basics’ reminders for what makes a warehouse effective & efficient. Whenever making changes/improvements within a warehouse environment it is worth referring to these principles to ensure you are not overlooking something.
1.Place most frequently picked items as close together
2.Minimise the need for elevated storage locations
3.Never travel empty
4.Create directional flow (clockwise-anti clockwise)
5.Minimise crossovers
6.Separate areas by compliment products E.G if picking tennis rackets, put tennis balls close by.
7.Maximise simple visual management principles
8.Simplify picking sheets/instructions as much as possible
9.Use simple, low cost automation to speed up picking. E.g. Hoppers, scales, measures
10.Minimise transport
11.Create flexible picking locations
Flow Racks
When are they effective?
​
Flow racks (also known as gravity feed racks and point of use racks) are extremely beneficial when utilised correctly, but more often than not a hinderance on productivity.
Flow racks are often seen as a ‘magical solution’ to provide pickers with a very high range of different products within a very small area. This is true, however they are extremely poor for overall space utilisation.
For example compare a standard pallet that can hold 360 cases of an item within the 1m x 1.2m x 1m = 1.2m3, Equating to 330cases per cubic metre. A flowrack containing the same item will hold roughly 60 cases per cubic metre.
For this exact reason, the type of product that is placed within flow racks is extremely important. They should contain items that are ordered in low volumes, with a large variety of different SKUs available. Flowracks should not contain a large quantity of the same SKU because the additional walking distance & high replenishment time associated with the very low density of items/m3 will outweigh the benefits.
​
Think of flow racks as the rows of houses in Amsterdam's cobbled streets. Flow-racks, just like Amsterdam's squeezed houses, accommodate a high number of small families/individuals within a small area. Not suited to large families due to the lack of space, but perfect for lots of different families and individuals to live a close proximity to the centre of town.
​
​
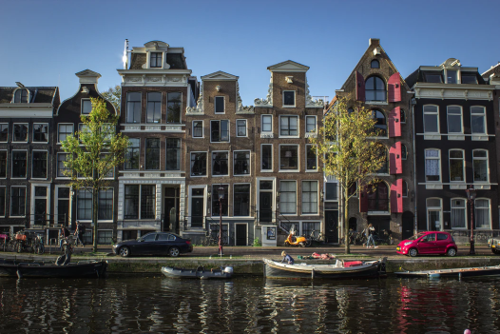
The reason I compare flow racks to Amsterdam in particular, is because in the 17th Century locals were taxed based on the width of their property on the street. Clever properties were designed to be wider at the rear and narrower at the front, thus giving the appearance of being small.
The same mindset of taxing the width of properties based on their width should be carried over to warehouse design. Each additional inch taken up on the roadside is space where a more beneficial product could be placed. Every additional inch of flow racks equates to additional time spent whenever walking past those racks and not using them. The benefits of having a high SKU density (large number of different families) needs to outweigh the ‘road tax’ that applies to them.
​
Benefits of Flow Racks
•Promotes FIFO
•Highly Ergonomic for the picker
•Can be restocked without interference with picker
•Very high SKU density (# of SKUs/volume)
Mock up design - The importance of offline testing
Prior to live, disruptive and costly changes, it is always best to test any warehouse solution in an offline environment, where alterations can be made and tested without risk. This can be achieved in a wide range of ways, varying in complexity and cost.
Starting with the simplest, the layout design/floorplan can be tested using chalk in a car park to test size restrictions etc. This is particularly useful when you are testing flows and measuring distances. For example if you wanted to test a clockwise flow vs an anti-clockwise flow, you could pick a typical order and compare the times, replicating the experiment to provide a fuller picture.
Another common method and one that is fast, can be done in 3 dimensions & is cost effective is to create a Lego mock-up. Although spending a day with Lego may appear like child's play, it is very useful to check any constraints and can be used to measure space utilisation as well as quickly try different layouts with ease. The beauty of using Lego is that you gather the opinions of all relevant stakeholders without them having to image what it may look like.
Lastly, simulation tools provide the most detailed, scenario based and data driven insights into the performance of layout designs. Being much more expensive than the other options, simulations are still relatively inexpensive when you calculate the potential savings, especially if you have an expert conduct the work for you. Additionally, simulation provides confidence in the results as they have become extremely accurate and complex, able to test a wide range of scenarios, restrictions and limits etc. From experience I would suggest a combination of the use of Lego, to first draft ideas and collect all opinions/suggestions. Once different suggestions have been consolidated, I would use simulation software to provide the results and confidence that the decision is the preferred solution.

Automation
Automation has come on a long way in the last 5 years. Every year, the adoption of automation is increasing and its capabilities expanding. Within warehouses, a wide variety of tasks occur, from un-palleting & inspecting the goods that arrive, transport to shelving using forklifts/pump trucks, order picking, labelling and truck loading to name a few. Automation is highly suited to a large proportion of roles when compared to many other industries. This is largely due to the repetitive and relatively simple nature of the processes. For example, transporting pallets to shelves can be completed with simple robots, labelling & wrapping can be done with simple robots and the scanning & warehouse management can be done with QR codes or NFC chips. Some industries are integrating automation into their warehouses at much faster rates than others.
​
At Ocados warehouse on the outskirts of Andover (UK) is something referred to as the hive or the grid. Within the warehouse is a team of over 1000 standardised robots, operating within what can be described as like a 3D chessboard. The robots are controlled via one central computer which conducts the complex algorithms that decide where to go, what to pick and where to return to. The simple tasks conducted by the robots include ‘lifting, moving, sorting, picking’, many of the simple jobs that are often done by humans. One great advantage of using these robots is the ability for items to be stored in positions without the requirement for memory. Unlike traditional warehouses, where operators become more efficient, the more familiar they become with the layout, here, an algorithm picks the optimum location to store items based on the frequency of use, where is available and current trends in demand etc. This means batteries might be stored on the location above fresh avocados on Monday and above bottles of wine on Tuesday. There is no need to ‘remember’ where items are placed.
​
Unlike other industries that have adopted automation, Ocado have cleverly focused their efforts on optimising and maintaining only 1 type of robot. This means every robot can be maintained in a standard way and the maintenance complexity is hugely reduced; boosting robot uptime & reducing costs.


Product Slotting - ABC Analysis
ABC analysis is a simple methodology for identifying what items move with the greatest frequency and what items move with the lowest frequency.
The items that have the highest frequency can then be placed in the most valuable positions (with the least transport distance from both ‘goods in’ and ‘dispatch’.
If you think of a warehouse almost like property within a city. The most expensive and valuable properties are those that are most central and close to hot-spots (in this case that is where the goods arrive and dispatch). There would be little point putting a product that rarely leaves into a valuable property because they wouldn’t maximise the benefit of reduced transport/movement that could have been achieved with a fast-moving product.
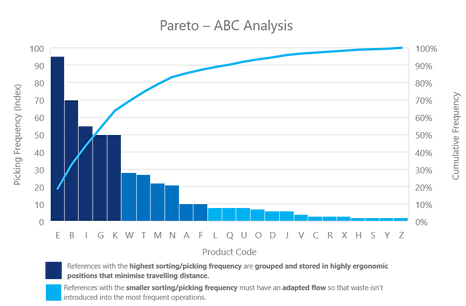
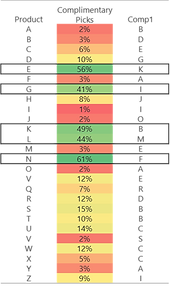
In order to develop a continuous improvement, learning culture, the organisation must move from firefighting to improvement support.
Many companies suffer from a phobia of raising problems and concerns. It is easier to put on a brave face, say that everything went perfectly well, and not learn from the callosal feedback and advice that has been provided. A shift in cultural behaviours is required, where problems can be openly raised and the voices of customers & employees are truly listened to and acted upon.
​
​
​
How do you help create a Learning Organisation?
​
One, guiding principle: provide a voice to all employees & the tools/support required to solve problems.
​
1)Voice to all employees
​
2)Tools required to solve problems
​
3)Support from superiors to solve the problems
Although ABC analysis is effective at identifying the high-level view of what items should be placed in which locations, the extent in which the true potential of product slotting can be achieved involves a combination of many different analysis methods.
Identifying complimentary picks is another highly effective method to be deployed alongside ABC analysis. The logic is; if I am often picking multiple items together, why not store them next to each other?
Organisation by Value Streams
•The different Value Streams inside a warehouse have a designated warehouse location;
•Each Value Stream has an its own operations specifications and equipment and productivity metrics;
•The target is to eliminate long trips and empty returns;
•Focus on the best customer service and short lead time.
•Simple timings using a stop watch can signify the improvements
