
Manufacturing
Industry
Achieve your growth aspirations with our transformation process
The FlowPlus™ transformation process
Over 20 UK Manufacturers have transformed their business with our 4-step process
1. DISCOVERY
By starting with a discovery phase, we understand your unique manufacturing process and the challenges you face - uncovering areas for improvement and your gap-to-potential.

Gain all the insight in one, concise, step by step assessment report.

01
Lean Maturity Audit
Assess your lean maturity across 25 categories including quality focus, efficiency, workplace organisation, data, technology, strategy, leadership, culture and more.
02
Performance Analysis
Great processes create great results, Simple but not easy.
We review your current processes to gain an in-depth understanding of existing pain-points, where information sharing and communication breaks down, waste steps that can be eliminated/automated.
03
Gap to potential analysis
Quantify the gap between your current state and desired state, understand what changes are needed to become best-in-class manufacturers
04
Implementation roadmap
Convert improvement actions into projects, and produce a bespoke improvement roadmap aligned with your company strategy.
2. ASSESSMENT
The Assessment phase investigates the unique solutions required to close your gap-to-potential and become a best-in-class manufacturer. Creating a bespoke implementation roadmap aligned with your strategic aims, we provide you with a practical step by step approach needed to get tangible results fast.
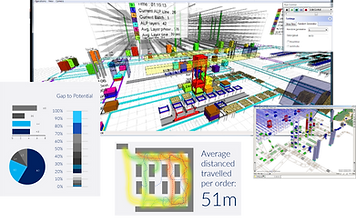
05
Customer Feedback Analysis
Using AI and advanced machine learning techniques, we will identify what your customers care most about and innovative ways of exceeding their expections.
06
Value Stream Mapping
Painting a clear picture of your manufacturing system, you will start to see the waste and improvement opportunties that have been hidden all this time.
07
Motion tracking
Quantify the waste of motion & transport with the latest technology. Find optimised layouts and floorplans by tracking products, people & forklifts.
08
Flow Analysis
There is often huge untapped potential when improving the flow of your system. Understand how to balance work and minimise lead time with our flow analysis tool.
3. IMPLEMENTATION
Implementation is what we pride ourselves on. We don't write reports and leave the hard part to you...We roll up our sleeves, get on the shopfloor and make the changes needed.
Working with the operators that know the processes best, we conduct workshops as one-team, until the target is achieved.
The solutions we implement are tailored to each client and their unique challenges. Examples range from re-designing and transforming a factory layout to maximise flow and improve efficiency, through to implementing kanban system that control stock levels.

40% reduction in Lead Time

30% improvement in productivity

45% reduction in internal quality defects

55% decrease in machine downtime
4. TRAINING
We offer both in-person & online training. Both training courses are deliberately different to other training providers in one main way:
Our training is practical & hands-on.
Our online training course has global recognition and has a review rating of 4.8/5 from over 5,000 active students.
Like the in-person training, the online courses provide you with the practical ability to apply the lean tools.
We have 5 different courses varying in complexity/commitment.
5000+
No of students we have trained globally
Modules:
-
What is Lean? (White Belt)
-
Introduction to Six Sigma (White Belt)
-
Identifying and Eliminating Waste (White Belt)
-
History of Lean (Yellow)
-
Kaizen (Yellow)
-
Change management & Paradigms (Yellow)
-
Flow, Batch Sizes, Push vs Pull & Takt
-
Visual Management (Yellow)
-
Spaghetti Diagrams (Yellow)
-
Value Stream Mapping (VSM)
-
Overall Equipment Effectiveness (OEE)
-
Standards & Standard Work
-
Total Productive Maintenance (TPM)
-
Quick Changeovers (SMED)
-
5s - Productive Workspaces
-
Collaborative Problem Solving, A3, 5Whys, Fishbone, Root Cause Analysis (RCA)
-
The DMAIC Process (White Belt)
-
Advanced DMAIC process
-
Taguchi Loss Function (Yellow)
-
Statistical Process Control (Yellow)
-
Kano Model
-
Quality Function Deployment
CASE STUDIES
A selection of success stories.
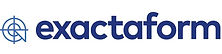





Textile Manufacturing
Implementing a data- driven TPM maintenance strategy
Reduced equipment downtime across site by over 75%.
Increased OEE of 37%

Tooling Manufacturing
Reduced Quality defects by over 80%
Used Six Sigma techniques to improve process robustness & stability.

Electronics Manufacturing
Increasing output capacity by >20%
Redesigning and implementing new ergonomic work stations

Packaging Manufacturing
Optimised inventory levels through Kanban
Reduced stock holding cost by £600,000 per year

TESTIMONIALS
FlowPlus have been a real help in our push to improve OEE, from helping to identify the areas that we needed to change to actually helping us improve.
Sean Tilley -
MD
We have been working with FlowPlus for the last three years and they have helped improve all parts of our business. We used to hold a considerable amount of WIP stock and have over the years have managed to reduce this to next to nothing, with most of our manufacturing line now single peice flow.
Ben Gibbons -
Factory Manager
Our teams really enjoy the workshop style that FlowPlus use. They feel like they have a say in the changes being made and are being heard which is refreshing change from previous consultancies we've worked with.
Anna Howles -
Production Manager